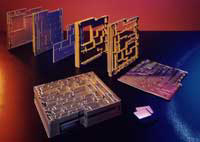
This highly accurate process is capable of casting fine detail with excellent surfaces
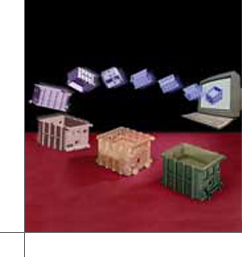
RP is the new, hip buzzword making its way around companies searching for that competitive edge. However, lessons can always be learned from the past, and two proven, mature metal casting processes have the power to unlock RP's true potential"
-Paul J. Armstrong, Armstrong RM Corp, USA
Two Steps Back
The main benefit of prototyping is design verification, providing the opportunity to identify design flaws before a product goes into production. The further along the developmental cycle design errors are discovered, the greater the cost to fix them. This is especially true for die cast components where tooling prices can run into six figures.
The cost of discovering design errors after the die cast tooling is complete can be even worse. The most obvious cost is tool rework. Seventy-five per cent of production dies require rework ranging from simple modifications to a major overhaul - a figure that is unacceptably high. Additional costs can include shorter tool life and late delivery of the product to the marketplace. At a minimum, a three-month delay in introducing the product to market means a loss of sales and a potential loss of market share that may be hard to recover. Appropriate use of today's prototyping technologies can help manufacturers avoid these needless added costs and uncomfortable situations.
There are many methods of prototyping die cast parts, but two of the most effective are plaster mold casting (also known as rubber plaster mold casting - or RPM) and rapid die casting from cast H-13 steel dies (also known as the Steele process). These two techniques play different roles.
Plaster mold provides initial prototype aluminum or zinc castings in a few weeks when starting with a Stereolithography (SLA) model. This low-cost 'soft' tooling approach usually costs about 10 per cent of production die cost. It allows for quick and easy modifications to part geometry. That ease of geometry modification facilitates design refinement. If required, the process is capable of manufacturing thousands of parts through the use of reusable silicon rubber foundry tooling.
Rapid die casting provides initial sample parts in five to eight weeks, depending on part geometry. The process starts with a SLA model and the casting of H-13 steel dies. This means prototypes are processed as a pressure die casting instead of a gravity-poured casting. Alloys, physical, and thermal properties will be the same as in the production run, while RPM uses slightly different alloys with different properties. Rapid die casting is the best method for providing short runs (up to several thousand) to enable production while final production dies are finished and qualified.
RPM and rapid die casting can be complimentary in many cases. RPM can provide initial samples in a shortened time frame while the part design is perfected. Cast dies can offer cost savings and increased production rates before full production tooling is completed.
PLASTER MOLD CASTING
Plaster mold casting is a quick and relatively inexpensive way of producing aluminum and zinc castings. SLA or other rapid models can be used as master models to develop tooling. The plaster process differs from the use of Quickcast (in which models are destroyed making each casting) in that plaster mold casting creates foundry tooling from the SLA model. Once the rubber tooling has been generated, it can be used to produce up to a thousand aluminum or zinc castings before tooling maintenance is required. Rubber foundry tooling may be cost justified over Quickcast even if only a few Quickcast models are required, depending on part complexity. For smaller quantities (less than five pieces), plaster molds can be made directly from many types of rapid prototyping models for geometries with or without side pulls. This approach is referred to as loose pattern molding.
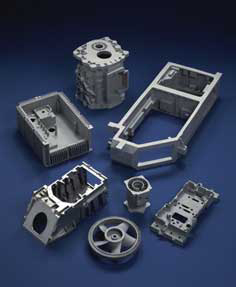
The plaster process has some invaluable properties, among them its ability to produce complex, thin-walled castings with excellent surface finishes. That makes it the ideal choice for reproducing the fine and complex details often found in SLA models. Casting lead times vary from a few days to several weeks depending on part complexity. It can cast a wide range of sizes but is most applicable to parts that fit within a 2- to 24-inch cube range. Quantities ranging from two or three pieces to several thousand pieces can be produced as functional die cast prototypes. Therefore, plaster serves as a bridge process while awaiting delivery of production tooling and, in many cases, as a production process where quantity requirements do not justify the expense of hard tooling.
Ideally, the production die caster and the plaster mold source should work closely with the end user to ensure a smooth transition between processes. Plaster mold casting can simulate any die castable geometry and it is critical that designers do not configure the RPM casting to a geometry that will increase die casting prices - or worse still, result in a shape that cannot be die cast.
THE PROCESS
The first step in the RPM process is to create a master model. Usually it is SLA but in many cases traditional pattern making models are still used. The parting lines are then established and negative molds are developed from the model. A silicon rubber positive is made from each of the negative molds. Gating runner systems are added as required. Next, a liquid plaster slurry is poured over the silicon rubber patterns. Once the plaster molds have set, they are removed from the rubber patterns and baked to remove moisture.
Subsequently, molten aluminum is poured into the assembled plaster mold. Once the metal has solidified, the plaster mold is destroyed so the part can be taken out. The reusable rubber tooling can make hundreds of molds. After the casting has passed initial inspection, gates and flash are removed and the part is now ready for secondary operations such as machining, assembly, chemical or paint finishes. Again, for time savings in creating a few pieces, plaster molds can be made directly from the SLA pattern once parting lines have been created.
RAPID Die Casting
Rapid die casting from cast tooling is an approach to die cast prototyping and short runs that has been around for several decades, but the advent of CAD and SLA modeling is driving a renewed interest into its application. Starting with a SLA model, H-13 steel dies are cast to a net shape in a fraction of the time required for cutting tool steel. Additional geometry can be added via secondary machining. The key benefit is that prototype parts are processed as a die casting and therefore physical and thermal transfer properties that will be identical to the production part. Additionally, this process can provide considerable cost advantage over RPM for quantities over a thousand. Since the components are run in a die cast press, large numbers of parts can be manufactured in a short amount of time.
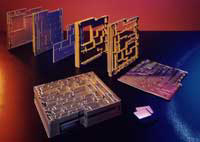
This highly accurate process is capable of casting fine detail with excellent surfaces. Complex parting lines can be accommodated, as well as side actions via hand loads. This approach is not recommended for use with thin, tall standing part detail or with cast-in water lines. Typical lead times range from five to eight weeks dependent on part size and complexity.
In the cast H-13 steel die process, an initial pattern is generated via SLA or CNC with shrinkage factors scaled in. Parting lines are developed and a soft durometer negative is created in the shape of the tool. A ceramic tool is made and the steel is poured. Cavity detail can be finished if required via CNC or EDM. The inserts are squared and fitted into a standard mold base where ejection pins are added. Gates and overflows are machined in and the cast die is ready to run in a standard die cast press. Parts can be run in any die cast alloy and finishing requires only a trim and any secondary machining that may be necessary.
ENHANCE COMPETITIVENESS
To remain competitive in today's markets, manufacturers are constantly searching for new benefits from prototyping that go far beyond the ability to assess the visual qualities of a design. Today, prototyping can enable actual functional, assembly and performance testing. Functional prototypes support more detailed market research to assess the viability of a product before a decision is taken to move to full scale production. All of this is made possible by prototypes that have the same or similar properties and materials as those of the production parts. As we have seen, two time-tested metal casting processes in combination with such new technologies as RP provide these benefits while accommodating today's time-compressed engineering requirements. The ability to use rapid prototypes as master patterns in both processes provides significant time and cost savings.