All of these options must be considered at the beginning of a program. Early involvement with a supplier is the key to allowing the customer's vision to become a successful reality.
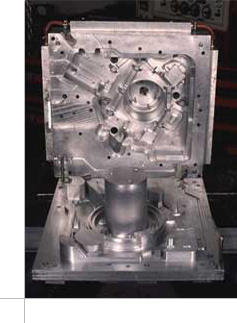
Reaction Injection Molding for Premium Polyurethane Parts.
"Over the last 20 years Reaction Injection Molding (RIM) has emerged as a popular method of producing premium quality molded polyurethane parts. These range from simple parts to complicated structural components, typically in volumes of one to 5,000 pieces. The case studies detailed here demonstrate that RIM is suitable for a wider range of applications than one would expect."
Dan O'Brien, Armstrong RM Corporation, USA
Two-part, low-viscosity urethane systems are easily processed and are available in a variety of hardness and stiffness ranges. Urethanes reproduce fine details, are dimensionally stable, chemical resistant, physically tough, and wear resistant. Excellent flowability allows the encapsulation of inserts. Considerable design freedom is possible with thick and thin wall sections due to the uniform shrink characteristics. Flame retardant grades with UL 94 VO and 5V are also available. Foamed polyurethanes are natural thermal and acoustic insulators controlled by adjusting the molded part density and choice of material system. RIM polyurethane parts are produced for a wide variety of industries, including medical, computers, business machines, telecommunications and graphic imaging.
Polyurethane Material
There are two broad categories used to describe plastic materials.
-Thermoplastics
Thermoplastics, described in simplistic terms, soften and melt when heated and harden when cooled, allowing the use of injection molding, thermoforming, extrusion, and other processing techniques.
-Thermosets
Thermosets form chemical bonds between adjacent polymer molecules, called crosslinking. This system of polymer chains tends to degrade instead of soften when subjected to extreme heat. Recent advances in recycling techniques have allowed breakdown and subsequent reuse of some base components. Because they do not melt, thermosets must be processed differently.
Some thermosets can be further polymerized by adding heat. Materials such as phenolics and epoxies can be injected or transferred into or compressed within a hot mold. RIM-molded polyurethanes require a controlled chemical reaction within the mold. Not only is a part made but the plastic material is also created as the mold becomes the polymerization reaction vessel with components impinged in a mix head as they enter.
Cycle times are generally longer, and parts require more secondary finishing than thermoplastics, but they usually shrink less and exhibit much better thermal and chemical resistance.
Polyurethanes can be broken down into two groups:
- Elastomeric or flexible systems range from almost rigid high modulus impact-resistant materials to super-soft and flexible polymers
- Rigid materials have a higher flexural modulus and hardness up to glass-like and very brittle materials.
Within these two groups, polyurethanes can be further broken down into three additional types of material systems.
- Foamed polyurethanes
Foamed polyurethanes use blowing agents to form a sandwich of high-density rugged skin and a lower density cellular core. Suitability for applications is influenced by system rigidity and cell size. - Solid polyurethanes
Solid polyurethanes are processed without blowing agents to form a homogeneous flexible or rigid plastic. Of any polyurethane category they exhibit the most thermoplastic-like properties and are used extensively in the automotive, agriculture and recreational industries. Thin-walled parts can be molded, making them valuable for prototype studies. - Composite systems
Composite systems can be foamed or solid, rigid or elastomeric, but are molded with fiber reinforcements, such as glass, to enhance the structural properties of the molded part. Stiffness and impact strength are enhanced by adding reinforcement in the material stream, (Reinforced RIM-RRIM), or by using a molded preform in the mold that is encapsulated, (Structural RIM-SRIM).
Another RIM-processed material showing some promising results for specific applications is polyurea. Modified resins, particularly those modified with rubber, show good stiffness and a dramatic improvement in impact strength. These resins remain more difficult to process because of the high component viscosities and the need for tighter control of resin and mold temperature.
TOOLING
The low internal mold pressure generated during the RIM process (100-200 psi) makes available a variety of choices when deciding on a mold material and construction technique:
- Silicone rubber can be quite successful when used for very low quantities of dimensionally non-critical parts;
- Resin molds are used for components requiring more detail and better physical properties. Foamed urethane systems can be processed in these urethane and epoxy resin molds;
- Spray metal molds offer better control of surface quality and offer enhanced moldability. This mold-building technique bridges the gap between low-volume prototype and medium production tooling, and is actually a composite system with an epoxy and aluminum chip mixture acting as the backup structure for the thin metal surface. Aluminum frames are usually cast to act as a mold base for mounting ejector systems, mix head, side pulls, and to ultimately mount to a production press;
- Aluminum must be used when maximum physical properties of the urethane material system are required. A properly cooled aluminum mold is best able to control the heat of reaction during the molding process and not allow exotherm overrun and hot spot induced internal stresses. When dimensional accuracy is critical and production quantities are high, machined aluminum is the logical choice, but cast aluminum, kirksite or nickel shell tooling should not be overlooked as an alternative. Their dimensional accuracy is only slightly less than a machined process and quite suitable for most applications.
This tooling can be generated using many of the current CAD data-generated rapid construction techniques. Stereolithography (SLA, 3D Systems), Selective Laser Sintering (SLS, DTM Corp), Laminated Object Manufacturing (LOM, Helisys) and Fused Deposition Modeling (FDM, Stratasys) are some of the rapid modeling methods used to make a master model for any of the previously mentioned soft tooling. Wood, polyurethane board, aluminum, and even blocks of thermoplastic material can be machine-cut using IGES compatible NC tool path cutting software. A technique often overlooked in this fast-paced world of computers is the handmade model. The customer can sometimes benefit by logically combining the best of the old and the new, forming a marriage that can often make the difference to a successful outcome.
All of these options must be considered at the beginning of a program. Early involvement with a supplier is the key to allowing the customer's vision to become a successful reality.
"Thirty prototypes had to be installed on working units in the field in nine weeks, and 100 units per week had to be available during the construction of the production thermoplastic mold."
CASE ONE
Encapsulation of a 5 ft long circuit board in RIM polyurethane for a commercial air traffic control radar antenna
Previous production attempts were very labor-intensive, did not give the boards consistently adequate protection from the outdoor environment, and did not yield the expected electronic performance. The success potential of the program was in question. The customer desperately needed a material and manufacturing method that totally encapsulated the fragile circuitry, remained radar transparent, and was more cost-effective. The need to isolate the circuit board completely from the effects of the outdoor environment indicated a process capable of one-shot encapsulation. The material chosen for initial testing was a high-density, foamed, RIM-processed polyurethane manufactured by the Bayer Corporation.
To minimize cost potential during the R&D phase, a small-scale cast urethane test mold was fabricated and some circuit boards supplied. It was clear after initial testing that material performance to specification was of prime importance.
Aluminum was chosen as a mold for its ability to cycle heat and also for allowing quick "on-the-fly" geometry changes.
The viability of the chosen material and processing was proved at least enough to justify the next phase, a full-size prototype to encapsulate a working circuit board. This phase was not without difficulty as the fragility of the circuit board during the molding operation and subsequent thermal performance testing presented the R&D team with numerous opportunities for improvement.
Ultimately, with the help of a couple of proprietary processing procedures, the RIM-processed polyurethane and its flowability, adjustable density, and exotherm during the molding process were key factors in the successful performance of this antenna.
CASE TWO
Prototyping for a thermoplastic structural foam housing and sunshield for a digital telephone system using high-density, rigid, foamed, RIM-processed polyurethane
For many reasons the mold and part construction phase of a project must start before the customer knows exactly what they want. In this case the part was originally designed as a sheet metal fabrication and the geometry redesign had not been completed. Thirty prototypes had to be installed on working units in the field in nine weeks, and 100 units per week had to be available during the construction of the production thermoplastic mold. This would mean that any mold made for the RIM phase of the project must last at least for 2,000 parts. In addition to this the parts also had to:
- Be able to closely match critical physical properties of the production material;
- Perform well enough in the field to eliminate the need for retrofit with production parts;
- Duplicate all geometries and features needed by the production molder;
- Allow for secondary machining and fabrication to add revision changes.
The molds produced for the RIM prototypes had to:
- Mold parts with minimal need for secondary finishing operations;
- Last for as many as 3,000 parts with minimal degradation;
- Be delivered on time and ready to run immediately.
A spray metal mold was chosen for the cover, and because the geometry was complete, a model was made using SLA. This model was made with added shrink and used as the mold pattern or master model. This allowed a concurrent and slightly different approach to producing the mold for the main housing.
As the design was not complete for the housing and the schedule was compressed, a handmade pattern was started with revision changes added on the fly. The upper part that formed an air vent chamber and included cover mount bosses had to be molded with a side pull. The schedule allowed this feature to wait for final geometry and an aluminum plug was machined out of solid and fitted to the spray metal section during final mold assembly. This decision also helped the long-term mold integrity and stability during the extended RIM prototype production phase.
CASE THREE
A low density thermal enclosure for a medical diagnostics application
Traditional manufacturing methods for this type of application have included the following:
- Hand applying a thermal wrap or blanket to a metal enclosure;
- Foam filling a metal casting with low-density foamed polyurethane;
- Injection molding a thermoplastic "shell" and foam filling later as a separate step;
- Premolding a core with low-density polyurethane, suspending this preform in a second mold and encapsulating it with a high-density polyurethane.
All of the above are currently being used for part-specific reasons, but this enclosure assembly had to be molded using a one-shot process. The parts had to have the proper insulating value, act as a unit substructure, encapsulate reinforcements and attachment features, allow secondary machining, and conform to an elevated visual standard. All of this with a material system originally designed as a non-visual insulator.
Once again the primary concern was to allow the material to meet or exceed its intended specification range. The only choice was to build machined aluminum molds for the production phase of the program. Some compromises were made for the prototype phase with some major parts of the molds being cast with polyurethane. Many revision changes were made during the testing phase. Mold sections cast in urethane made these changes relatively easy. A low-density rigid urethane system manufactured by Stepan and originally developed for the fine furniture industry accommodated the combined need for structure, surface appearance and thermal insulation.
Reference:
Bayer Corporation: Engineering Polymers Material Selection, Thermoplastics and Polyurethane, A Design Guide