"The specific properties of the RIM process, the properties of the Bayer materials and creative moldmaking combined to allow technically sound performance, short lead times and attractive economics."
R.I.M. - REACTION INJECTION MOLDING
Innovative approach to part design enables maximum performance for Affymetrix® GeneChip® product.
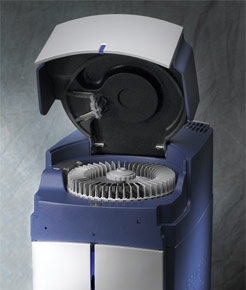
Published in The TCT Magazine
Affymetrix of Santa Clara, CA is the industry pioneer that invented the first microarray and scanner. The GeneChip® Scanner 3000 is a laser scanning, fluorescent colifocal microscope scanner that can read Affymetrix® GeneChip arrays containing up to 2.5 million biological features. Its scan rate is about 2 times that of any other system.
The auto-loading feature allows for automated, unattended walk-away operation of up to 48 arrays. Affymetrix designed the GeneChip AutoLoader as an add-on to the existing Scanner 3000. The AutoLoader provides a temperature-controlled environment, giving long-term stability for the samples in queue for up to 16 hours. Pre-scan and post-scan arrays are held at a constant 15° C.
The need for low temperature insulation combined with structural needs along with cosmetic appeal enabled Armstrong RM of East Syracuse, NY to consider a combination of materials, tooling approaches and specific processing opportunities that their RIM (Reaction Injection Molded) Process can offer. The AutoLoader consists of four unique RIM polyurethane composite parts.
- The main housing needed to provide structure for mounted internal and external components, a surface to allow a paint coating for outside visual appeal and most importantly, for function, it would provide the required thermal insulation performance
- The door had to provide all of the above and have additional visual quality and toughness to the exposed insulation layer
- The remaining two components are internal non-visual functional parts
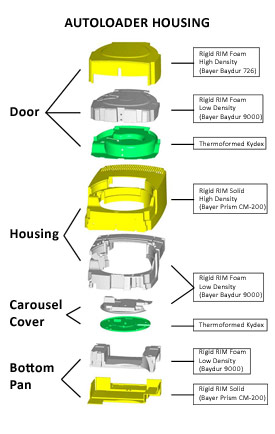
Bayer Prism CM-200 was chosen as the material for structural shell of the main housing and internal parts, each having the need for a 1/8" wall and 94VO rating. Bayer Baydur 726 was chosen as the structural skin of the door with its nominal 1/4"? wall and UL flammability rating. Each of these skins has a second layer of Baydur 9000 low-density rigid foam molded at 6 lb/ft(ft) (ft). The low-density foam is molded directly to the skin on the main housing. For the door, Armstrong RM came up with an innovative solution for the exposed insulation: molding the Baydur 9000 low-density foam to a thermoformed Kydex skin and then assembling this structure to the molded 726 door after the painting operation is finished. The carousel cover completes the assembly with Baydur 9000 being molded to a Kydex skin.
To facilitate the overmolding processes, a variety of tooling approaches were utilized on the different components. On the main housing, both molds were cast in Kirksite ( Zinc/ Aluminum alloy). Stereolithography master patterns or negatives were created and the Cast Kirksite molds were poured from them using the Plaster Mold casting process. On the remaining parts, tooling was made either by CNC cutting aluminum or using a SLA master to make epoxy resin moulds. Armstrong RM has developed many different tooling methods over the years and then applies the best tooling approach for each application.
The specific properties of the RIM process, the properties of the Bayer materials and creative moldmaking combined to allow technically sound performance, short lead times and attractive economics.